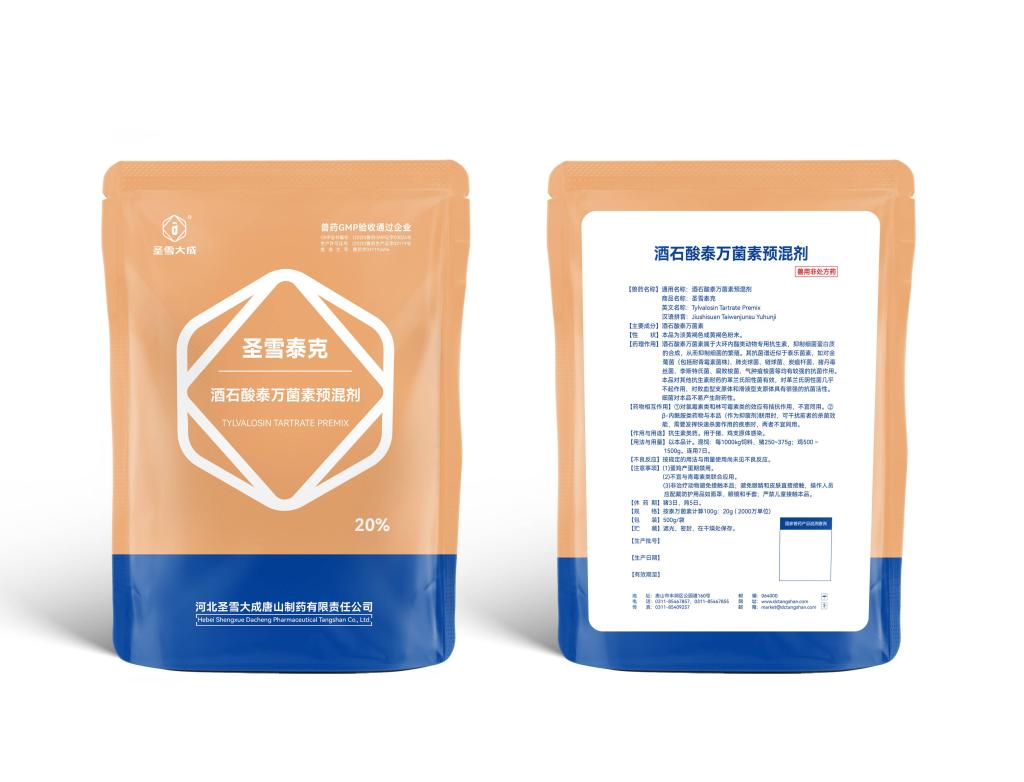
Tylvalosin tartrate is an important antibiotic used in veterinary medicine, particularly for the prevention and treatment of bacterial infections in livestock. As a macrolide antibiotic, it is effective against a range of Gram-positive and Gram-negative bacteria. The formulation of tylvalosin tartrate into premix feeds involves complex processes that require stringent quality control measures to ensure efficacy, safety, and regulatory compliance. This article explores the quality control measures involved in the production of tylvalosin tartrate premix formulations, highlighting key aspects from raw material selection to final product testing.
The Importance of Quality Control in Tylvalosin Tartrate Premix Formulations
Quality control (QC) is crucial in the production of tylvalosin tartrate premix formulations due to several factors:
Efficacy: Ensuring that the premix contains the correct concentration of tylvalosin tartrate is essential for therapeutic effectiveness.
Safety: Proper QC prevents contamination and ensures that the product is safe for consumption by livestock.
Regulatory Compliance: Adherence to regulatory standards is required to meet legal and industry-specific guidelines.
Effective quality control measures help to maintain the integrity of the product throughout its lifecycle, from manufacturing to end-use.
Raw Material Quality Control
1. Selection and Testing of Raw Materials
Before production begins, the selection of high-quality raw materials is fundamental to the quality of the final premix. This includes:
Tylvalosin Tartrate: The active pharmaceutical ingredient (API) must be sourced from reputable suppliers and must meet strict purity and potency standards. Testing includes:
Identity Tests: Confirm the API’s chemical structure and verify its identity.
Purity Tests: Ensure that the tylvalosin tartrate is free from impurities and contaminants.
Potency Tests: Confirm that the API meets the required concentration specifications.
Excipient Materials: These are substances used to aid in the formulation of the premix, including carriers, binders, and fillers. Testing includes:
Purity and Safety: Ensure that excipients are free from contaminants and suitable for animal consumption.
Compatibility: Verify that excipients do not react adversely with tylvalosin tartrate.
2. Supplier Qualification
Suppliers of raw materials must be qualified through a rigorous process that includes:
Audit and Inspection: Regular audits and inspections of supplier facilities to ensure compliance with good manufacturing practices (GMP).
Certification: Ensuring suppliers have relevant certifications (e.g., ISO 9001) indicating adherence to quality standards.
Manufacturing Process Quality Control
1. Formulation and Mixing
The formulation of tylvalosin tartrate premix involves precise blending of the API with excipients. Key QC measures include:
Weighing Accuracy: Accurate measurement of tylvalosin tartrate and excipients to ensure the correct dosage in the final product.
Mixing Uniformity: Ensuring thorough and uniform mixing to achieve a consistent distribution of the API throughout the premix. Techniques such as high-shear mixing and blending are used, and the process is monitored for consistency.
2. Granulation and Milling
In some formulations, granulation and milling are necessary to achieve the desired particle size and consistency. QC measures include:
Granule Size Analysis: Monitoring particle size distribution to ensure uniformity and optimize bioavailability.
Flowability Tests: Ensuring that granules have appropriate flow properties for efficient handling and mixing.
3. Stability Testing
Stability testing is crucial to ensure that the premix maintains its efficacy and safety over its shelf life. Testing includes:
Accelerated Stability Testing: Exposing samples to elevated temperatures and humidity to predict long-term stability.
Real-Time Stability Testing: Monitoring samples under normal storage conditions to observe any changes in potency, appearance, or safety over time.
In-Process Quality Control
1. Environmental Monitoring
Maintaining a controlled manufacturing environment is essential for preventing contamination. This includes:
Air Quality Monitoring: Ensuring that the air in the production area is free from particulates and microbial contamination.
Surface Cleanliness: Regular cleaning and sanitization of equipment and surfaces to prevent cross-contamination.
2. In-Process Testing
Testing during the production process helps to detect and address any issues promptly. In-process testing includes:
Intermediate Testing: Analyzing samples at various stages of production to ensure adherence to quality specifications.
Visual Inspection: Checking for physical defects or inconsistencies in the premix, such as clumping or uneven coloring.
Final Product Quality Control
1. Analytical Testing
The final premix product undergoes a series of analytical tests to ensure it meets all specifications:
Potency Testing: Confirming the concentration of tylvalosin tartrate to ensure it is within the specified range.
Purity Testing: Ensuring that the final product is free from impurities and contaminants.
Microbial Testing: Testing for the presence of microbial contaminants to ensure the product is safe for animal consumption.
2. Physical Characteristics Testing
Testing for physical characteristics ensures the product meets the desired specifications:
Appearance: Evaluating color, texture, and consistency of the premix.
Bulk Density: Measuring the bulk density to ensure uniformity in the premix.
3. Packaging and Labeling
Quality control extends to the packaging and labeling of the premix:
Packaging Integrity: Ensuring that packaging materials are suitable and do not affect the product’s quality.
Label Accuracy: Verifying that labels accurately reflect the product’s contents, dosage instructions, and any regulatory information.
Regulatory Compliance and Documentation
1. Regulatory Standards
Compliance with regulatory standards is essential for the approval and sale of tylvalosin tartrate premix formulations. This includes:
Good Manufacturing Practices (GMP): Adhering to GMP guidelines to ensure product quality and safety.
Regulatory Approvals: Obtaining necessary approvals and certifications from regulatory bodies such as the U.S. Food and Drug Administration (FDA) or European Medicines Agency (EMA).
2. Documentation and Record Keeping
Accurate documentation is vital for maintaining quality and ensuring traceability:
Batch Records: Detailed records of each batch’s production process, including raw materials, formulation steps, and testing results.
Quality Control Reports: Documentation of all QC tests and their results, including any corrective actions taken.
Challenges and Innovations in Quality Control
1. Emerging Technologies
Innovations in analytical and monitoring technologies are enhancing quality control processes:
Real-Time Monitoring: Advanced sensors and real-time monitoring systems allow for continuous tracking of production parameters and early detection of deviations.
Automated Testing: Automation of analytical testing and in-process monitoring increases efficiency and reduces the risk of human error.
2. Global Standards
As regulations and standards evolve globally, manufacturers must stay updated on international requirements to ensure compliance across different markets.
3. Sustainability Considerations
Sustainable practices in the production of tylvalosin tartrate premix formulations are becoming increasingly important. This includes reducing waste, optimizing resource use, and implementing environmentally friendly processes.
Conclusion
Quality control in the production of tylvalosin tartrate premix formulations is essential for ensuring product efficacy, safety, and regulatory compliance. The rigorous QC measures applied throughout the production process—from raw material selection to final product testing—are crucial for maintaining high standards and protecting animal health.