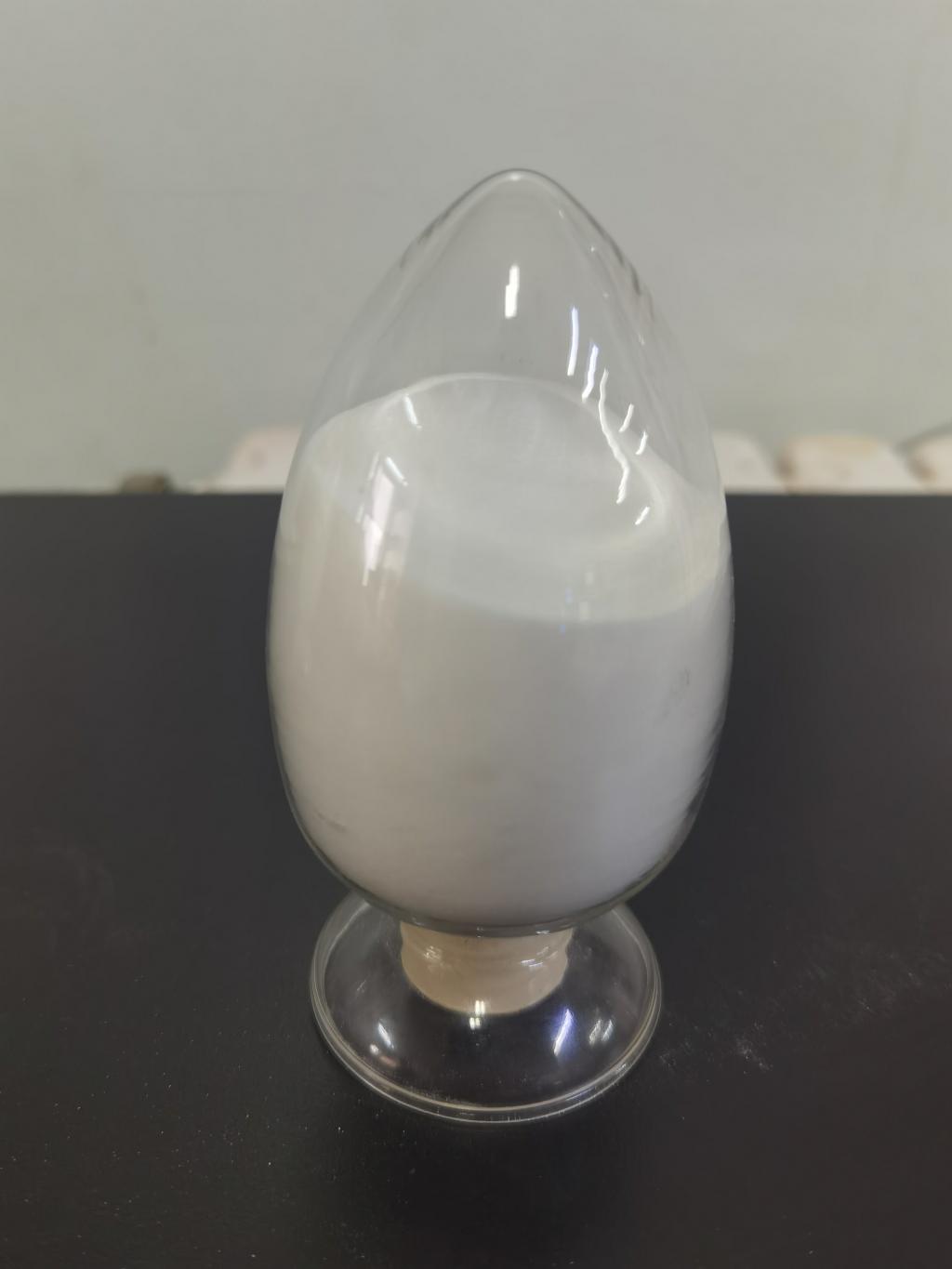
ε-Polylysine hydrochloride, a cationic biopolymer renowned for its antimicrobial properties, has garnered significant attention across various industries. From food preservation to pharmaceutical formulations, its effectiveness against a broad spectrum of microorganisms makes it a valuable asset. However, the commercial viability of ε-Polylysine hydrochloride hinges on the scalability of its production processes. This article explores the importance of scalability and the strategies employed to ensure efficient and cost-effective production of ε-Polylysine hydrochloride.
Understanding ε-Polylysine Hydrochloride:
Before delving into scalability, it's essential to grasp the fundamentals of ε-Polylysine hydrochloride production. This biopolymer is derived from the fermentation of Streptomyces albulus, a process involving microbial cultivation and downstream processing steps. The resulting ε-Polylysine hydrochloride is then purified and formulated for various applications, including food preservation, pharmaceuticals, and cosmetics.
Importance of Scalability:
Scalability refers to the ability to increase production output while maintaining efficiency and cost-effectiveness. For ε-Polylysine hydrochloride to achieve widespread adoption and commercial success, its production processes must be scalable to meet growing demand and achieve economies of scale. Factors such as production yield, process efficiency, and cost per unit play crucial roles in determining the scalability of ε-Polylysine hydrochloride production.
Optimizing Fermentation Processes:
Fermentation is the cornerstone of ε-Polylysine hydrochloride production, where Streptomyces albulus strains are cultivated in bioreactors under controlled conditions. Scaling up fermentation processes involves optimizing parameters such as temperature, pH, oxygen supply, and nutrient availability to maximize biomass and ε-Polylysine hydrochloride production. Advanced monitoring and control systems are employed to ensure reproducibility and consistency at larger scales.
Downstream Processing Efficiency:
Following fermentation, ε-Polylysine hydrochloride is recovered and purified through downstream processing steps, including cell separation, extraction, purification, and formulation. Scalability in downstream processing relies on the implementation of efficient separation and purification techniques that can handle increased volumes of fermentation broth. Continuous processing systems and automation technologies are adopted to streamline operations and minimize processing times.
Cost-Effective Raw Material Sourcing:
The scalability of ε-Polylysine hydrochloride production is also influenced by the availability and cost of raw materials. Key components such as fermentation substrates, nutrients, and energy sources must be sourced cost-effectively to ensure profitability at larger scales. Sustainable sourcing practices and strategic partnerships with suppliers help mitigate raw material procurement challenges and ensure a reliable supply chain.
Process Integration and Optimization:
To enhance scalability, ε-Polylysine hydrochloride production processes can be integrated and optimized for efficiency and resource utilization. Integration of unit operations, such as fermentation, downstream processing, and formulation, reduces processing steps and minimizes product loss. Furthermore, continuous improvement initiatives, such as lean manufacturing and Six Sigma methodologies, drive efficiency gains and cost savings.
Modular Design and Flexibility:
Scalability is facilitated by the modular design of production facilities, allowing for incremental expansion and adaptation to changing production requirements. Flexibility in equipment layout, process flow, and capacity enables seamless scale-up without significant disruptions to ongoing operations. Modular bioreactor systems and flexible processing equipment enhance agility and responsiveness to market demand fluctuations.
Compliance with Regulatory Standards:
As ε-Polylysine hydrochloride is intended for use in food, pharmaceutical, and cosmetic applications, compliance with regulatory standards is paramount. Scalable production processes must adhere to Good Manufacturing Practices (GMP) and regulatory requirements established by authorities such as the U.S. Food and Drug Administration (FDA) and the European Medicines Agency (EMA). Robust quality management systems and documentation practices ensure product safety and regulatory compliance at all production scales.
Continuous Innovation and Research:
Achieving scalability in ε-Polylysine hydrochloride production requires ongoing innovation and research efforts to optimize processes, improve efficiency, and address emerging challenges. Investments in research and development enable the discovery of novel strains, fermentation techniques, and purification technologies that enhance productivity and reduce production costs. Collaboration with academic institutions and industry partners fosters knowledge exchange and accelerates technological advancements.
Market Dynamics and Demand Forecasting:
Scalability considerations are influenced by market dynamics and demand forecasting. Comprehensive market analysis helps anticipate future demand trends and identify opportunities for expansion or diversification. Market-driven strategies guide investment decisions and resource allocation, ensuring alignment with customer needs and market expectations.
Conclusion:
The scalability of ε-Polylysine hydrochloride production processes is a critical factor for its commercial viability and widespread adoption across industries. Optimization of fermentation processes, efficiency in downstream processing, cost-effective raw material sourcing, process integration, compliance with regulatory standards, and continuous innovation are key elements in achieving scalability. By investing in scalable production infrastructure, technology, and expertise, manufacturers can meet growing demand, achieve economies of scale, and capitalize on the diverse applications of ε-Polylysine hydrochloride.