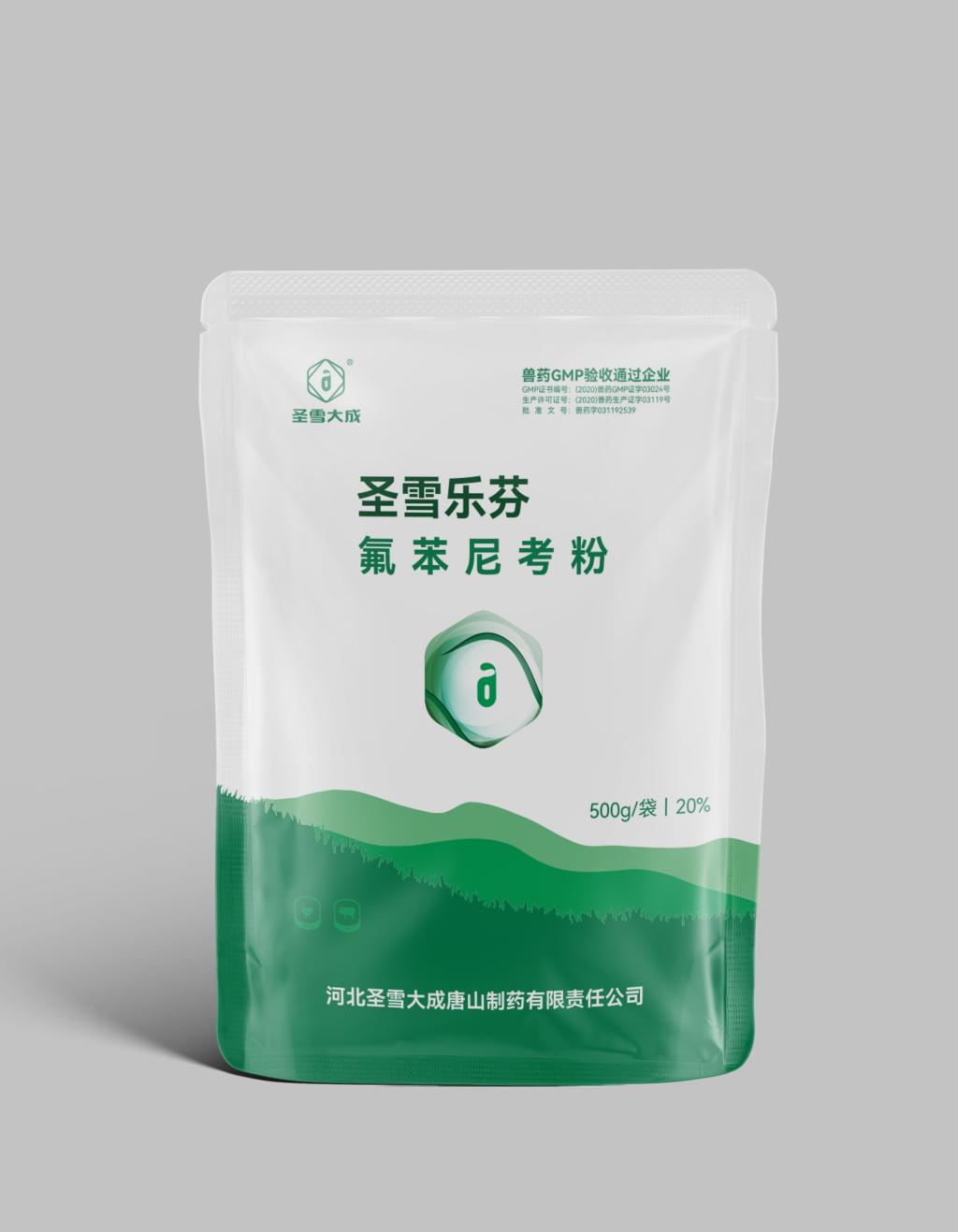
Florfenicol, a broad-spectrum antibiotic, is widely used in veterinary medicine to treat bacterial infections in livestock. The efficacy and safety of florfenicol powder are heavily dependent on the quality of its manufacturing process. To ensure that the product meets the necessary standards for purity, potency, and safety, stringent quality control (QC) measures must be implemented throughout the manufacturing process. This article explores the key quality control measures that are essential in the production of florfenicol powder, highlighting the importance of these measures in maintaining product integrity and regulatory compliance.
Understanding Florfenicol Powder
Florfenicol is a synthetic derivative of thiamphenicol, known for its effectiveness against both Gram-positive and Gram-negative bacteria. It is commonly used in the treatment of respiratory, gastrointestinal, and other bacterial infections in various animal species, including cattle, swine, and poultry. Florfenicol powder is typically formulated for oral administration through feed or water, or for parenteral use by injection. The quality of the final product is critical to ensure that it delivers the intended therapeutic benefits without causing harm to the animals or contributing to antimicrobial resistance.
Key Quality Control Measures
To maintain the highest standards of quality, the following QC measures are typically implemented during the manufacturing of florfenicol powder:
Raw Material Inspection and Testing: Before the manufacturing process begins, all raw materials, including the active pharmaceutical ingredient (API) and excipients, must be thoroughly inspected and tested. This includes verifying the identity, purity, and physical properties of the materials. Techniques such as high-performance liquid chromatography (HPLC), infrared spectroscopy (IR), and mass spectrometry (MS) are commonly used to ensure that the materials meet the required specifications.
In-Process Controls (IPC): During the manufacturing process, in-process controls are implemented to monitor and control the quality of the product at various stages. IPCs may include checks on particle size, uniformity, and homogeneity of the mixture. These controls help to identify and correct any deviations from the standard operating procedures (SOPs) before they can affect the final product.
Environmental Monitoring: The manufacturing environment must be controlled to prevent contamination. Regular monitoring of air quality, temperature, humidity, and microbial levels is essential. Cleanroom conditions, as specified by Good Manufacturing Practices (GMP), are maintained to ensure that the manufacturing area is free from contaminants that could compromise the product's quality.
Equipment Calibration and Maintenance: All equipment used in the manufacturing process, including mixers, sieves, and packaging machines, must be regularly calibrated and maintained to ensure their proper functioning. Calibration ensures that the equipment operates within the specified tolerances, while maintenance prevents breakdowns and reduces the risk of cross-contamination.
Batch Record Review and Documentation: Detailed batch records are maintained to document every step of the manufacturing process. These records include information on the raw materials used, in-process controls, environmental conditions, and the results of all tests performed. Batch records are reviewed and approved by the quality assurance (QA) department to ensure that the product was manufactured according to the established procedures and meets the required standards.
Finished Product Testing: Once the manufacturing process is complete, the finished product undergoes a series of tests to confirm its identity, strength, and purity. These tests may include HPLC, IR, and UV-visible spectroscopy to verify the API content and to check for impurities. Microbial testing is also performed to ensure that the product is free from harmful microorganisms.
Stability Testing: Stability studies are conducted to determine the shelf life of the product under various storage conditions. These studies involve storing samples of the product at different temperatures and humidity levels and periodically testing them for changes in physical, chemical, and microbiological properties. The results of stability testing are used to establish the expiration date and storage conditions for the product.
Packaging and Labeling Controls: Proper packaging and labeling are crucial to protect the product from degradation and to provide accurate information to the end-user. Packaging materials must be compatible with the product and provide adequate protection against light, moisture, and other environmental factors. Labels must clearly indicate the product name, strength, batch number, expiration date, and other relevant information, as required by regulatory authorities.
Regulatory Compliance and Certification
Compliance with international and local regulations is a fundamental aspect of quality control in the manufacturing of florfenicol powder. Key regulatory frameworks and certifications include:
Good Manufacturing Practices (GMP): GMP guidelines, established by regulatory authorities such as the U.S. Food and Drug Administration (FDA) and the European Medicines Agency (EMA), set out the minimum requirements for the manufacture, testing, and release of pharmaceutical products. Adherence to GMP is mandatory for the approval and marketing of florfenicol powder.
ISO Certification: Many manufacturers seek ISO 9001 certification, which provides a framework for an effective quality management system. ISO 9001 certification demonstrates a commitment to continuous improvement and customer satisfaction.
Product Registration and Approval: Florfenicol powder must be registered and approved by the relevant national regulatory authority in each country where it will be marketed. The registration process involves submitting detailed dossiers that include information on the product's composition, manufacturing process, and quality control data.
Conclusion
The implementation of robust quality control measures is essential in the manufacturing of florfenicol powder to ensure that the product is safe, effective, and compliant with regulatory standards. From the inspection of raw materials to the final packaging and labeling, each step in the manufacturing process must be carefully controlled and monitored. By adhering to GMP and other regulatory requirements, manufacturers can produce a high-quality product that meets the needs of veterinarians and farmers, ultimately contributing to the health and well-being of animals. As the demand for high-quality veterinary medicines continues to grow, the commitment to rigorous quality control remains a cornerstone of the industry.