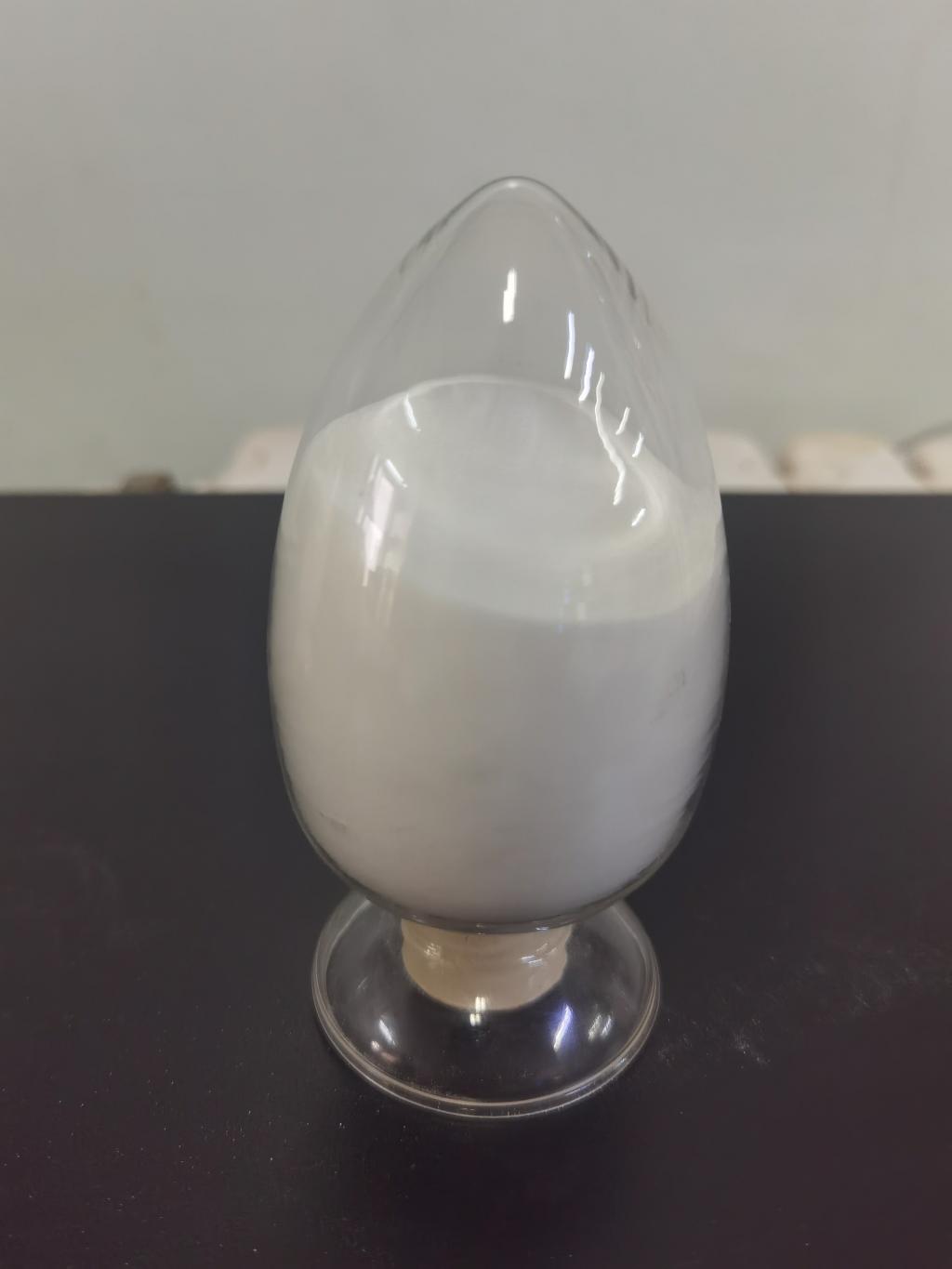
As the food industry increasingly shifts towards natural and sustainable practices, ε-polylysine hydrochloride (ε-PL) has emerged as a prominent natural antimicrobial agent. Produced through the fermentation of Streptomyces albulus, ε-PL offers significant advantages in food preservation due to its broad-spectrum antimicrobial properties and safety profile. However, like any industrial process, its production involves environmental considerations that must be evaluated to ensure its overall sustainability.
This article explores the environmental impact and sustainability of ε-polylysine hydrochloride production. We will examine the various stages of its production process, assess the environmental implications, and discuss strategies and innovations aimed at enhancing sustainability.
Production Process of ε-Polylysine Hydrochloride
The production of ε-polylysine hydrochloride involves several key steps: fermentation, extraction, purification, and formulation. Understanding these stages is crucial for assessing the environmental impact and sustainability of ε-PL production.
1. Fermentation
The production of ε-PL begins with the fermentation of Streptomyces albulus, a bacterium that naturally produces the polypeptide. The fermentation process typically involves the following steps:
Inoculation: Streptomyces albulus is cultured in a growth medium containing nutrients such as carbohydrates, amino acids, and minerals. The choice of medium can significantly impact the efficiency and yield of ε-PL production.
Fermentation: The inoculated medium is incubated under controlled conditions (temperature, pH, and oxygen levels) to promote the growth of Streptomyces albulus and the production of ε-PL. This stage can last several days to weeks, depending on the specific strain and process parameters.
Harvesting: Once the fermentation is complete, the ε-PL is extracted from the fermentation broth. This involves separating the ε-PL from the microbial biomass and other components.
2. Extraction and Purification
After fermentation, ε-PL is extracted and purified to achieve the desired purity and quality. The extraction process typically involves:
Filtration: The fermentation broth is filtered to remove solid residues, including the microbial biomass.
Precipitation and Centrifugation: ε-PL is precipitated from the solution, often using salt or other chemicals, and then separated by centrifugation.
Purification: The precipitated ε-PL is further purified through processes such as ion exchange chromatography, dialysis, and crystallization to remove impurities and obtain a high-purity product.
3. Formulation and Packaging
The purified ε-PL is formulated into its final product form, which may include powder, solution, or other formulations suitable for use in food products. The final product is then packaged for distribution and use.
Environmental Impact of ε-Polylysine Hydrochloride Production
The environmental impact of ε-polylysine hydrochloride production can be assessed through various factors, including resource consumption, emissions, waste generation, and energy use.
1. Resource Consumption
Raw Materials: The production of ε-PL requires various raw materials, including growth media components, chemicals for extraction and purification, and packaging materials. The sourcing and consumption of these materials can impact the environment through resource depletion and ecological disruption.
Water Usage: The fermentation, extraction, and purification stages require significant amounts of water. Water usage can have environmental implications, especially in regions with water scarcity. Efficient water management practices are essential to minimize the environmental impact.
Energy Consumption: The fermentation process, as well as extraction and purification, involves energy-intensive operations. Energy consumption can contribute to greenhouse gas emissions, depending on the energy sources used. Transitioning to renewable energy sources and improving energy efficiency are important for reducing the carbon footprint of ε-PL production.
2. Emissions
Greenhouse Gas Emissions: The fermentation process and associated energy use can lead to greenhouse gas emissions, including carbon dioxide (CO₂) and methane (CH₄). These emissions contribute to climate change and should be minimized through energy-efficient practices and the use of renewable energy.
Air Pollution: The production process may also result in the release of volatile organic compounds (VOCs) and other pollutants. Proper ventilation and air filtration systems can help mitigate air pollution and improve environmental safety.
3. Waste Generation
Biological Waste: The fermentation process generates biological waste, including spent microbial biomass and residual growth media. Proper disposal or treatment of this waste is necessary to prevent environmental contamination. Composting or anaerobic digestion can be used to manage biological waste effectively.
Chemical Waste: Extraction and purification involve the use of chemicals, which can generate chemical waste. Managing and disposing of chemical waste in accordance with regulatory standards is crucial to minimize environmental impact.
Packaging Waste: The formulation and packaging stages generate packaging waste, which can contribute to environmental pollution if not managed properly. Recycling and using environmentally friendly packaging materials can help reduce packaging waste.
Strategies for Enhancing Sustainability
To address the environmental impact of ε-polylysine hydrochloride production, several strategies and innovations can be implemented to enhance sustainability.
1. Sustainable Raw Material Sourcing
Green Chemistry: Utilizing green chemistry principles in the production process can reduce the use of hazardous chemicals and improve overall sustainability. For example, using environmentally friendly solvents and reagents can minimize the environmental impact of the extraction and purification stages.
Renewable Resources: Sourcing raw materials from renewable resources, such as plant-based growth media components, can reduce the environmental footprint of ε-PL production. Sustainable agriculture practices and responsible sourcing are essential for minimizing resource depletion and ecological disruption.
2. Energy Efficiency and Renewable Energy
Energy-efficient Technologies: Implementing energy-efficient technologies and practices in the fermentation, extraction, and purification stages can reduce overall energy consumption. This includes optimizing process conditions, improving equipment efficiency, and recovering and reusing energy.
Renewable Energy: Transitioning to renewable energy sources, such as solar, wind, or hydroelectric power, can significantly reduce greenhouse gas emissions associated with ε-PL production. Investing in renewable energy infrastructure and integrating it into production facilities can enhance sustainability.
3. Water Management
Water Recycling: Implementing water recycling and reuse practices can reduce the overall water consumption in the production process. Treating and recycling process water for reuse in fermentation or other stages can minimize water wastage and reduce environmental impact.
Efficient Water Use: Adopting water-efficient technologies and practices, such as low-flow systems and water-saving equipment, can help minimize water usage and reduce the strain on local water resources.
4. Waste Management and Reduction
Waste Minimization: Reducing waste generation through process optimization and material efficiency can help minimize environmental impact. Implementing waste reduction strategies, such as lean manufacturing practices, can improve overall sustainability.
Recycling and Disposal: Proper recycling and disposal of waste materials, including biological and chemical waste, are essential for minimizing environmental pollution. Adopting recycling programs and adhering to regulatory standards for waste management can enhance environmental stewardship.
Valorization of Waste: Exploring opportunities for waste valorization, such as converting waste into valuable by-products or energy, can contribute to a circular economy and reduce environmental impact. For example, utilizing spent microbial biomass as a feedstock for bioenergy production or composting can add value to waste materials.
5. Life Cycle Assessment (LCA)
Conducting LCA: Performing a life cycle assessment (LCA) of ε-PL production can provide a comprehensive evaluation of its environmental impact. LCA assesses the entire life cycle of a product, from raw material extraction to end-of-life disposal, and helps identify areas for improvement in sustainability.
Continuous Improvement: Using LCA results to inform and guide continuous improvement efforts can enhance the environmental performance of ε-PL production. Regularly reviewing and updating sustainability practices based on LCA findings can drive ongoing progress towards environmental goals.
Innovations and Future Directions
Several innovations and emerging trends are shaping the future of ε-polylysine hydrochloride production and its environmental sustainability.
1. Advanced Fermentation Technologies
Bioprocess Optimization: Advances in bioprocess optimization, such as high-density fermentation and continuous fermentation, can improve the efficiency and yield of ε-PL production. These technologies can reduce resource consumption and waste generation, contributing to overall sustainability.
Synthetic Biology: The application of synthetic biology and genetic engineering techniques to modify Streptomyces albulus or other microorganisms can enhance ε-PL production. This approach can lead to more efficient production processes and reduced environmental impact.
2. Green Chemistry Innovations
Eco-friendly Reagents: Developing and using eco-friendly reagents and solvents in the extraction and purification stages can minimize environmental impact. Innovations in green chemistry can lead to more sustainable production processes and reduced chemical waste.
Biocatalysis: Employing biocatalysis techniques, such as enzyme-mediated reactions, can improve the efficiency and selectivity of production processes. Biocatalysis can reduce the need for harsh chemicals and minimize environmental impact.
3. Sustainable Packaging Solutions
Eco-friendly Packaging: Exploring and adopting eco-friendly packaging solutions, such as biodegradable or recyclable materials, can reduce packaging waste and environmental impact. Sustainable packaging practices can complement efforts to enhance the overall sustainability of ε-PL production.
Minimalist Packaging: Reducing packaging material use through minimalist packaging designs can help minimize waste and environmental footprint. Implementing packaging reduction strategies can contribute to a more sustainable production process.
4. Collaboration and Industry Initiatives
Collaborative Efforts: Collaborating with industry stakeholders, research institutions, and environmental organizations can drive innovation and sustainability in ε-PL production. Industry initiatives and partnerships can facilitate the sharing of best practices and the development of sustainable solutions.
Certification Programs: Participating in certification programs, such as those focused on environmental management and sustainability, can demonstrate commitment to sustainable practices and enhance credibility in the market.
Conclusion
The production of ε-polylysine hydrochloride involves several stages, each with its own environmental impact. Assessing and addressing these impacts is crucial for ensuring the overall sustainability of ε-PL production. By implementing strategies such as sustainable raw material sourcing, energy efficiency, water management, waste reduction, and life cycle assessment, the environmental footprint of ε-PL production can be minimized.