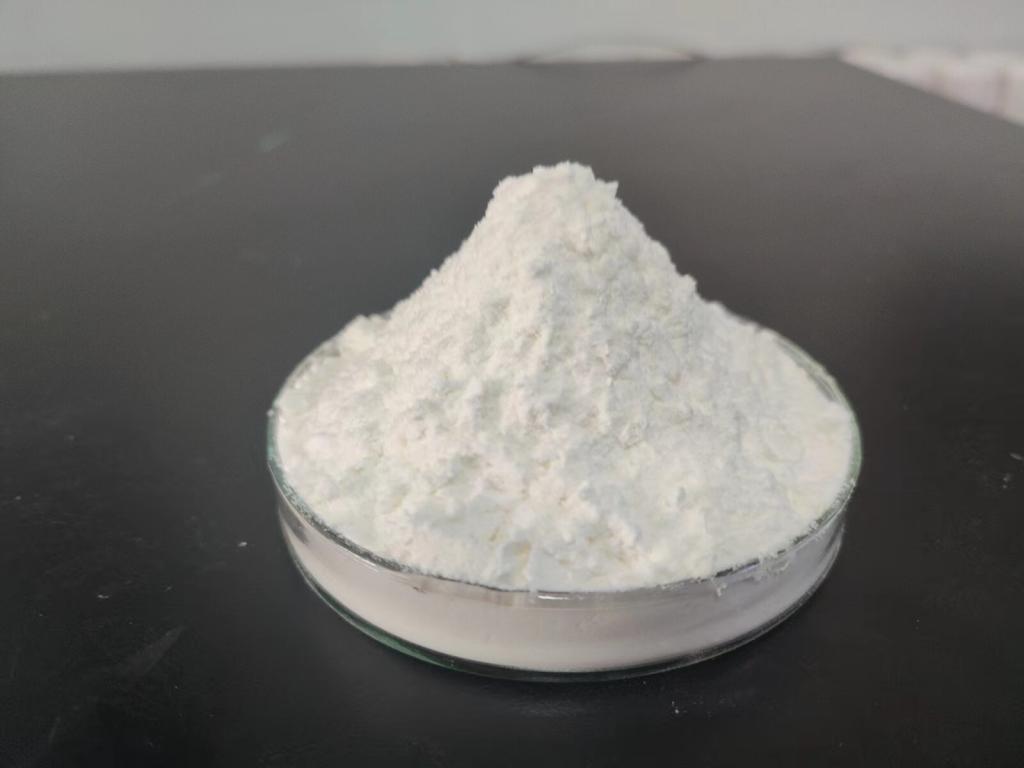
The demand for
ε-polylysine hydrochloride (ε-PL) has surged in recent years due to its diverse applications in pharmaceuticals, food preservation, and biomedical research. However, large-scale production of ε-PL presents a unique set of challenges, ranging from microbial fermentation optimization to downstream processing and purification. In this comprehensive review, we explore the key challenges and opportunities in the large-scale production of ε-PL, along with innovative strategies and technologies driving advancements in this field.
Overview of ε-Polylysine Hydrochloride Production
Microbial Fermentation:
ε-PL is primarily produced through microbial fermentation using strains of Streptomyces albulus or other ε-polylysine-producing microorganisms.
Fermentation processes involve the cultivation of microbial strains in suitable growth media under controlled conditions to maximize ε-PL production.
Downstream Processing:
After fermentation, ε-PL is recovered from the fermentation broth through a series of downstream processing steps, including cell separation, product extraction, and purification.
Downstream processing aims to isolate ε-PL from the fermentation broth and remove impurities to obtain high-purity ε-PL suitable for commercial applications.
Challenges in Large-Scale Production
Strain Selection and Optimization:
Identifying high-yield ε-PL-producing strains and optimizing fermentation conditions are critical steps in large-scale production.
Strain stability, productivity, and robustness under industrial fermentation conditions are key factors influencing ε-PL yield and production efficiency.
Fermentation Process Optimization:
Optimizing fermentation parameters such as temperature, pH, oxygen supply, and nutrient availability is essential for maximizing ε-PL production while minimizing production costs.
Balancing microbial growth and ε-PL biosynthesis rates to achieve high product yields without compromising cell viability is a major challenge in large-scale fermentation.
Product Recovery and Purification:
Developing efficient and cost-effective methods for ε-PL recovery and purification is a significant challenge in large-scale production.
Conventional methods such as solvent extraction, precipitation, and chromatography may require optimization to achieve high product yields and purity levels.
Innovative Strategies and Technologies
Genetic Engineering and Strain Improvement:
Genetic engineering techniques can be used to enhance ε-PL production by modifying metabolic pathways, increasing precursor availability, or improving strain tolerance to fermentation stresses.
Rational strain design and directed evolution approaches offer opportunities to engineer ε-PL-producing strains with superior productivity and fermentation performance.
Process Intensification and Automation:
Process intensification strategies, such as fed-batch and continuous fermentation, can increase ε-PL production rates and volumetric productivities.
Automation and control systems enable real-time monitoring and optimization of fermentation parameters, leading to more consistent product quality and higher production yields.
Novel Extraction and Purification Methods:
Advancements in extraction and purification technologies, such as membrane filtration, aqueous two-phase extraction, and adsorption chromatography, offer alternatives to traditional methods.
Integrated process designs combining multiple separation techniques can streamline ε-PL purification processes and reduce processing times and costs.
Opportunities for Expansion and Market Growth
Diversification of Applications:
The expanding applications of ε-PL in pharmaceuticals, cosmetics, personal care products, and food preservation create opportunities for market growth and product diversification.
Leveraging ε-PL's antimicrobial, preservative, and biocompatible properties, manufacturers can tap into new market segments and product categories.
Global Market Expansion:
Growing consumer awareness of food safety and demand for natural preservatives drive the global market for ε-PL and related products.
Strategic partnerships, distribution agreements, and market expansion initiatives can help manufacturers penetrate new geographic regions and target diverse customer segments.
Research and Development Investments:
Continued investments in research and development are essential for driving innovation and expanding the applications of ε-PL in various industries.
Collaborative research initiatives between academia, industry, and government agencies can accelerate technological advancements and address key challenges in ε-PL production and utilization.
Regulatory Considerations and Quality Assurance
Regulatory Compliance:
Meeting regulatory requirements and quality standards is paramount for ε-PL manufacturers to ensure product safety, efficacy, and compliance with regulatory guidelines.
Conducting thorough safety assessments, toxicity studies, and product testing is essential for obtaining regulatory approvals and market authorizations.
Quality Control and Assurance:
Implementing robust quality control and assurance systems throughout the production process is critical for maintaining product quality, consistency, and purity.
Analytical methods, process monitoring, and quality management systems help identify and mitigate potential risks and deviations in ε-PL production.
Conclusion
Large-scale production of ε-polylysine hydrochloride presents both challenges and opportunities for manufacturers seeking to meet the growing demand for this versatile biopolymer. By addressing key challenges in strain selection, fermentation optimization, and downstream processing, and leveraging innovative strategies and technologies, manufacturers can enhance production efficiency, increase product yields, and improve product quality. Seizing opportunities for market expansion, diversification of applications, and research and development investments further drives advancements in ε-PL production and accelerates its adoption in various industries. Through collaboration, innovation, and strategic planning, the large-scale production of ε-polylysine hydrochloride continues to evolve, paving the way for its widespread utilization in pharmaceuticals, food preservation, and biomedical applications.