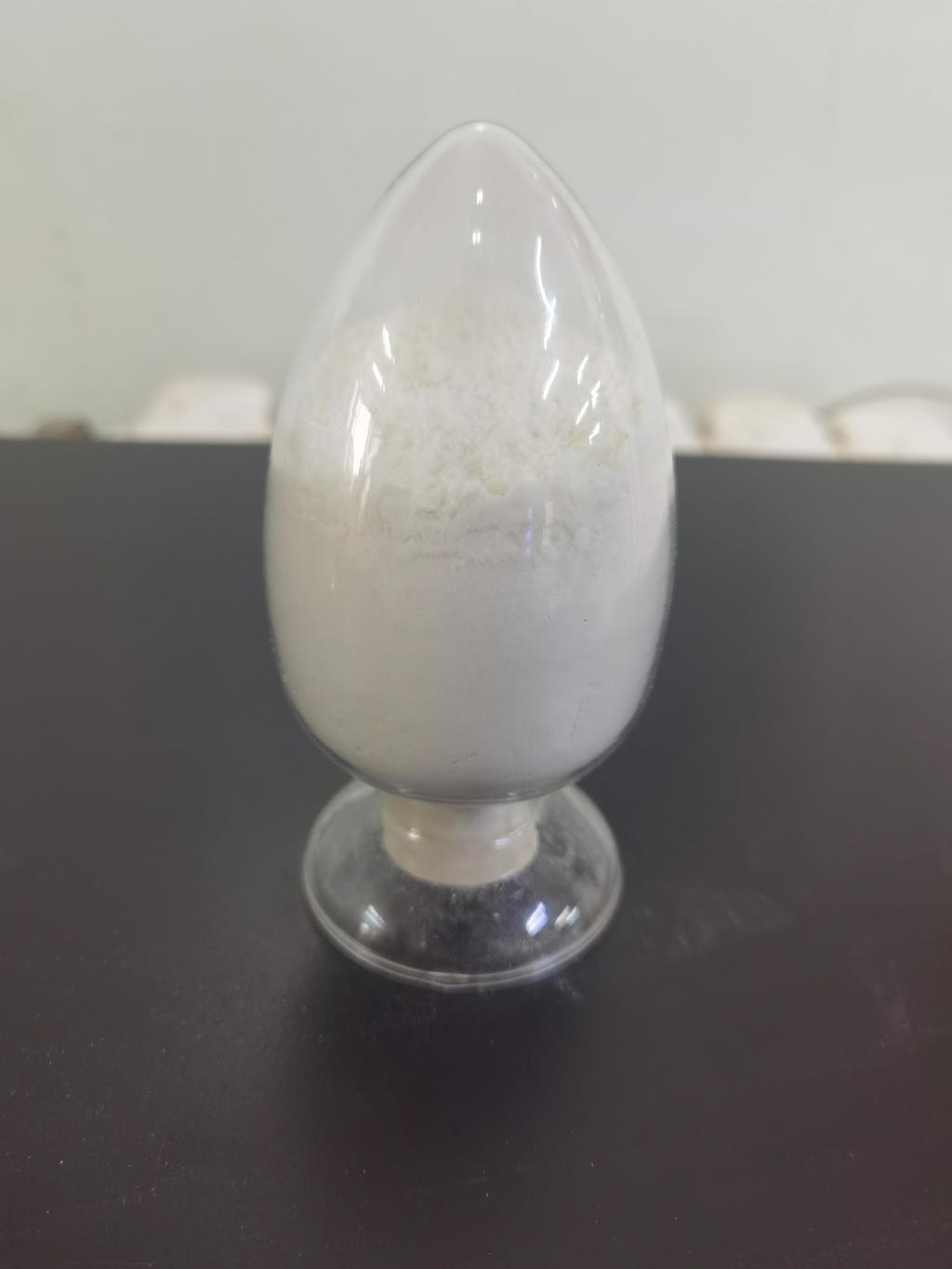
ε-Polylysine hydrochloride is a naturally occurring antimicrobial peptide known for its effectiveness in preserving food and enhancing product safety. Its broad-spectrum activity against bacteria, molds, and yeasts has made it an attractive alternative to synthetic preservatives in various industries, particularly food and cosmetics. As demand for natural preservatives continues to rise, advancements in the production and purification of ε-Polylysine hydrochloride are crucial for meeting industrial needs. This article explores the latest developments in the production processes, purification techniques, and the implications for industrial applications.
Production Techniques
Fermentation Processes: The primary method for producing ε-Polylysine involves fermentation using specific strains of bacteria, predominantly Streptomyces albulus. Recent advancements have focused on optimizing fermentation conditions to enhance yield and efficiency. Key parameters include:
Nutrient Optimization: Tailoring nutrient compositions, such as carbon and nitrogen sources, has been shown to significantly affect the growth of Streptomyces and the subsequent yield of ε-Polylysine. The use of inexpensive agricultural by-products as substrates is gaining attention for cost-effective production.
Bioreactor Design: Innovations in bioreactor technology, including stirred-tank reactors and fed-batch systems, have improved aeration and mixing, promoting optimal microbial growth and metabolite production.
Genetic Engineering: Advances in genetic engineering techniques, such as CRISPR and metabolic engineering, hold promise for enhancing the productivity of ε-Polylysine-producing strains. By manipulating metabolic pathways, researchers aim to increase the yield and efficiency of ε-Polylysine synthesis, thereby reducing production costs.
Co-culture Systems: Exploring co-culture systems where Streptomyces is combined with other microbial species can enhance the production of ε-Polylysine. These systems can create synergistic effects that optimize growth conditions and metabolite production.
Purification Techniques
The purification of ε-Polylysine is critical for ensuring its safety and efficacy in industrial applications. Recent advancements in purification methods include:
Precipitation and Filtration: Traditional purification methods often involve solvent precipitation and filtration. However, advancements in this area have led to improved recovery rates and purity levels. Techniques such as ammonium sulfate precipitation can selectively isolate ε-Polylysine from fermentation broths, allowing for easier downstream processing.
Chromatographic Methods: High-performance liquid chromatography (HPLC) and ion-exchange chromatography are increasingly being utilized for the purification of ε-Polylysine. These methods offer high resolution and specificity, enabling the separation of ε-Polylysine from other peptides and impurities. Recent innovations in chromatographic media and methods have further improved purification efficiency.
Membrane Filtration: Membrane technologies, including ultrafiltration and nanofiltration, have emerged as effective purification techniques. These methods can separate ε-Polylysine based on molecular size, providing a gentle and efficient means of concentrating and purifying the peptide while preserving its functionality.
Process Integration: Integrating production and purification steps into a continuous process can significantly enhance overall efficiency. By combining fermentation, separation, and purification in a streamlined workflow, manufacturers can reduce processing time and costs while improving product consistency.
Implications for Industrial Applications
The advancements in the production and purification of ε-Polylysine have significant implications for its industrial use:
Cost-Effectiveness: Improved production methods and purification techniques can lower the overall cost of ε-Polylysine, making it more accessible for food manufacturers seeking natural preservatives.
Quality Assurance: Enhanced purification methods ensure higher purity levels, which is crucial for regulatory compliance and consumer safety. This is particularly important in industries such as food, where safety and quality are paramount.
Market Expansion: As the production process becomes more efficient and cost-effective, the use of ε-Polylysine is expected to expand beyond food preservation into cosmetics, pharmaceuticals, and biotechnological applications.
Conclusion
Advances in the production and purification of ε-Polylysine hydrochloride are paving the way for its broader industrial use. Through optimized fermentation processes, innovative purification techniques, and the integration of modern biotechnological approaches, ε-Polylysine can be produced more efficiently and at a lower cost. These developments not only enhance the economic viability of ε-Polylysine but also position it as a valuable natural preservative in a variety of applications, meeting the growing consumer demand for safe and sustainable products.