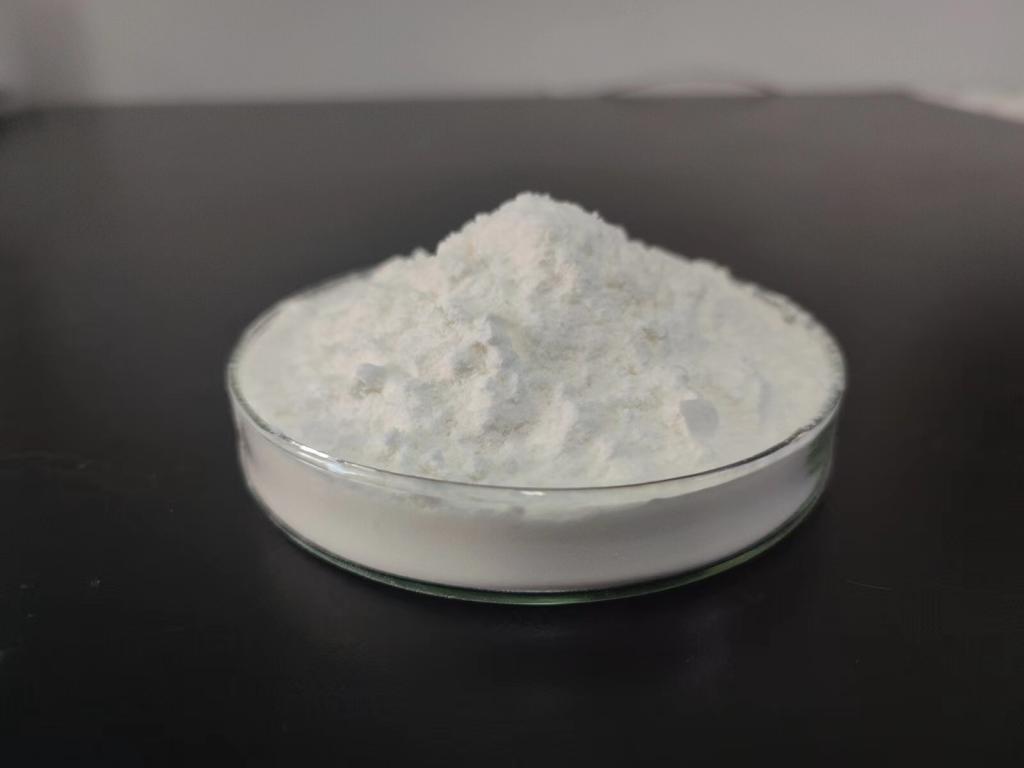
Microbial contamination poses a significant challenge in pharmaceutical manufacturing, where maintaining strict hygiene standards is crucial to ensure product quality, safety, and efficacy. Contaminated pharmaceutical products not only jeopardize patient health but also lead to costly recalls, regulatory penalties, and damage to brand reputation. In recent years, there has been increasing interest in
ε-polylysine hydrochloride (ε-PL) as a potential solution for reducing microbial contamination in pharmaceutical manufacturing processes. This article explores the impact of ε-PL on microbial contamination control in pharmaceutical manufacturing and its role in ensuring pharmaceutical product quality and safety.
Understanding Microbial Contamination in Pharmaceutical Manufacturing
Microbial contamination in pharmaceutical manufacturing refers to the presence of microorganisms, such as bacteria, fungi, and viruses, in pharmaceutical products or manufacturing environments. Contamination can occur at various stages of the manufacturing process, including raw material handling, formulation, filling, packaging, and storage. Common sources of microbial contamination in pharmaceutical manufacturing include:
Raw Materials: Contaminated raw materials, such as active pharmaceutical ingredients (APIs), excipients, and packaging components, can introduce microbial contaminants into pharmaceutical products during manufacturing.
Environment: Poorly controlled manufacturing environments, including air handling systems, cleanrooms, and equipment surfaces, can harbor microbial contaminants and facilitate their spread to pharmaceutical products.
Personnel: Human operators, including manufacturing staff, technicians, and quality control personnel, can inadvertently introduce microbial contaminants through improper hygiene practices, such as inadequate handwashing or improper gowning.
Water Systems: Contaminated water used in pharmaceutical manufacturing processes, such as for cleaning, sterilization, and formulation, can serve as a source of microbial contamination and compromise product quality.
ε-Polylysine Hydrochloride as a Microbial Control Agent
ε-Polylysine hydrochloride (ε-PL) is a natural antimicrobial agent produced by fermentation of Streptomyces albulus. It consists of a chain of lysine amino acids and exhibits broad-spectrum antimicrobial activity against bacteria, yeasts, and molds. In pharmaceutical manufacturing, ε-PL offers several potential benefits for controlling microbial contamination:
Antimicrobial Properties: ε-PL's antimicrobial activity helps inhibit the growth of a wide range of microorganisms, including bacteria, fungi, and viruses, in pharmaceutical products and manufacturing environments. This reduces the risk of microbial contamination and ensures product quality and safety.
Stability and Compatibility: ε-PL is stable under a wide range of pH, temperature, and environmental conditions, making it suitable for use in various pharmaceutical formulations and manufacturing processes. It is compatible with most commonly used pharmaceutical excipients and does not adversely affect product stability or efficacy.
Low Toxicity and Safety: ε-PL is generally recognized as safe (GRAS) for use in food and pharmaceutical applications and has low toxicity to humans and animals. It does not pose significant health risks or produce harmful byproducts, making it a safe and effective antimicrobial agent for pharmaceutical manufacturing.
Regulatory Acceptance: ε-PL has received regulatory approval for use as a food preservative and antimicrobial agent in several countries, demonstrating its safety and efficacy for use in pharmaceutical manufacturing. It is listed in regulatory databases, such as the United States Food and Drug Administration's (FDA) Generally Recognized as Safe (GRAS) list, as a permitted food additive.
Impact of ε-Polylysine Hydrochloride on Microbial Contamination Control
Preventive Measures: Incorporating ε-PL into pharmaceutical formulations and manufacturing processes helps prevent microbial contamination and reduce the risk of product recalls, quality deviations, and regulatory non-compliance. By inhibiting microbial growth, ε-PL ensures the integrity and safety of pharmaceutical products throughout their lifecycle.
Enhanced Product Stability: ε-PL helps maintain product stability by controlling microbial contaminants that can degrade active ingredients, compromise formulation integrity, and accelerate product degradation. This extends product shelf life, reduces the need for preservatives, and enhances product efficacy and performance.
Environmental Control: ε-PL contributes to maintaining clean and controlled manufacturing environments by minimizing microbial contamination on equipment surfaces, air handling systems, and facility infrastructure. This reduces the risk of cross-contamination and ensures compliance with good manufacturing practices (GMP) and regulatory requirements.
Cost Savings: By preventing microbial contamination and associated quality issues, ε-PL helps pharmaceutical manufacturers avoid costly production delays, rejections, and recalls. This results in significant cost savings and operational efficiencies, improving overall profitability and competitiveness in the pharmaceutical industry.
Challenges and Considerations
While ε-polylysine hydrochloride shows promise for reducing microbial contamination in pharmaceutical manufacturing, several challenges and considerations must be addressed:
Formulation Compatibility: ε-PL's compatibility with pharmaceutical formulations, including its stability, solubility, and interaction with other ingredients, must be evaluated to ensure optimal performance and efficacy in specific applications.
Regulatory Compliance: Pharmaceutical manufacturers must ensure that the use of ε-PL complies with regulatory requirements, including safety, efficacy, and labeling considerations. This may involve obtaining regulatory approval or conducting additional safety studies to support ε-PL's use in pharmaceutical products.
Quality Assurance: Robust quality control measures are essential to ensure the consistency, purity, and efficacy of ε-PL-containing pharmaceutical products. This includes testing for microbial contamination, potency, and stability throughout the manufacturing process and product lifecycle.
Consumer Acceptance: Communicating the benefits and safety of ε-PL-containing pharmaceutical products to healthcare professionals, regulatory authorities, and consumers is important for building trust and acceptance. Transparent labeling and clear communication about ε-PL's role in microbial contamination control can help educate stakeholders and promote acceptance of ε-PL-based pharmaceuticals.
Conclusion
ε-Polylysine hydrochloride (ε-PL) offers significant potential for reducing microbial contamination in pharmaceutical manufacturing, thereby enhancing product quality, safety, and regulatory compliance. By inhibiting microbial growth, ε-PL helps prevent product spoilage, degradation, and contamination, ensuring the integrity and efficacy of pharmaceutical products throughout their lifecycle. However, addressing formulation compatibility, regulatory compliance, quality assurance, and consumer acceptance is essential for realizing the full potential of ε-PL in pharmaceutical manufacturing. By embracing ε-PL and other innovative antimicrobial agents, the pharmaceutical industry can advance microbial contamination control practices and improve patient outcomes.